Silisyum karbürün (SiC) yarı iletken cihazlarda geniş çapta uygulanmasıyla birlikte, silikon karbür alt tabakaların kalite gereksinimleri giderek daha sıkı hale geliyor. SiC cihazları, yüzey kalınlığı değişimi, yüzey pürüzlülüğü (Ra), işleme hasarı ve astar filminin artık gerilimi konusunda katı düzenlemelere sahiptir. Bununla birlikte, kesme ve sıyırma sonrasında SiC alt katmanında sıklıkla hasarlı katman, yüksek yüzey pürüzlülüğü ve zayıf düzlük gibi sorunlar görülür. Sonraki epitaksi işlemi için yüksek kaliteli cilalı levha elde etmek için bu sorunların etkili düzleştirme işlemiyle çözülmesi gerekir. Bu makale, SiC alt tabaka düzleştirme prosesindeki taşlama ve taşlama teknolojisine odaklanacak ve bunların avantajlarını ve dezavantajlarını karşılaştırıp analiz edecektir.
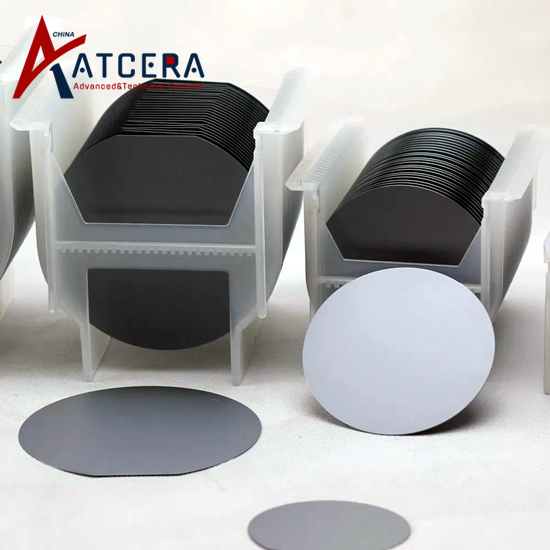
1. Taşlama işleminin mevcut durumu ve sınırlamaları
Taşlama işlemi, kaba taşlama ve ince taşlama olmak üzere iki aşamalı olmak üzere pazarda yüksek bir paya sahiptir ve kimyasal mekanik parlatmadan (CMP) önce tek taraflı mekanik parlatma (DMP) gerektirir. Avantajı, maliyetinin nispeten düşük olmasıdır, ancak hantal süreçler, düşük otomasyon düzeyi, yüksek parçalanma riski, düşük esneklik ve çevreye belirli etkiler gibi dezavantajları da vardır.
2. Taşlama işleminin avantajları ve uyarlanabilirliği
Öğütme işlemine alternatif olarak taşlama işlemi, daha yüksek talaş kaldırma oranları ve levha kalınlığı ve düzlüğünün daha iyi kontrolünü sağlar. Daha ince ve daha düzgün bir yüzey işlemi elde etmek için elmas taşlama diskleri gibi farklı aşındırıcılar ve taşlama teknikleri kullanılır. Öğütme işlemi otomasyon ve esneklik açısından mükemmeldir, tek talaş işlemeye uygundur ve büyük boyutlu levhaların işleme ihtiyaçlarına daha iyi uyum sağlayabilir.
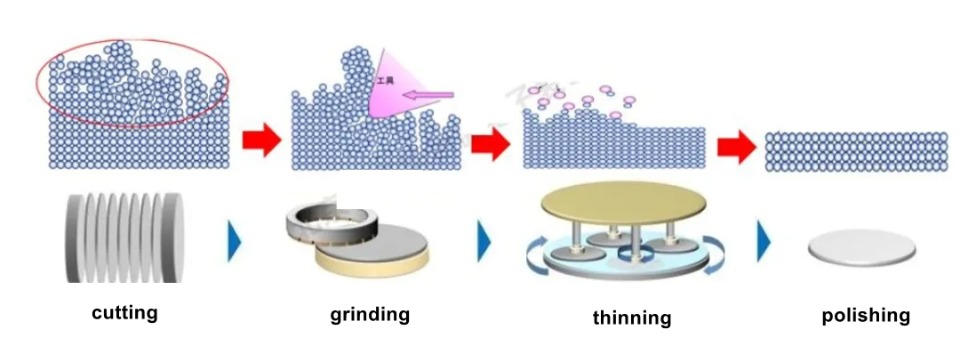
SiC alt tabaka düzleştirme işlem diyagramı
Öğütme işlemi genellikle kaba öğütme ve ince öğütme olmak üzere iki aşamayı içerir ve alt tabaka yüzeyinin hasarlı tabakası, yüzey düzgünlüğünü iyileştirmek için aşındırıcı malzemenin farklı parçacık boyutlarıyla kademeli olarak uzaklaştırılır. Ancak sürecin birçok sorunu var. Her şeyden önce, kaba öğütmeden ince öğütmeye, DMP ve CMP'ye kadar olan süreç daha karmaşıktır ve birden fazla adım gerektirir, bu da işlem süresini ve maliyetini artırır. İkinci olarak otomasyon düzeyi yüksek değildir ve bu da üretim verimliliğinin düşük olmasına neden olur. Büyük levhalar için işleme sırasında mekanik stres nedeniyle yüksek parçalanma riski vardır. Ayrıca, taşlama işleminin esnekliği düşüktür, bu da tek talaş işlemeye elverişli değildir ve taşlama sıvısının kullanımının çevre üzerinde belirli bir etkisi vardır.
Taşlama işleminde, SiC alt tabakaların daha yüksek talaş kaldırma oranlarıyla hızlı bir şekilde düzleştirilmesini sağlamak için elmas diskler gibi yüksek verimli aşındırıcılar kullanılır. Öğütme işlemiyle karşılaştırıldığında öğütme işleminin aşağıdaki avantajları vardır: birincisi, yüksek derecede otomasyon, üretim verimliliğini önemli ölçüde artırabilir; İkincisi, tek parça işlemeye uygun, iyi esnekliktir ve farklı ihtiyaçlara göre özelleştirilebilir; Üçüncüsü, büyük boyutlu levhaların işleme ihtiyaçlarına daha iyi uyum sağlayabilir ve parçalanma riskini azaltabilir. Ayrıca taşlama işlemi daha ince ve daha düzgün bir yüzey kalitesi sağlayarak sonraki CMP işlemleri için daha iyi bir alt tabaka sağlar.
Özetle, SiC alt tabaka düzleştirme prosesindeki taşlama ve taşlama tekniklerinin avantaj ve dezavantajları bulunmaktadır. Öğütme prosesinin maliyeti düşük olmasına rağmen proses hantaldır, otomasyon seviyesi yüksek değildir, parçalanma riski yüksektir ve esneklik düşüktür, bu da daha fazla gelişmesini sınırlamaktadır. Buna karşılık, öğütme işlemi otomasyon, esneklik, malzeme kaldırma oranı ve yüzey işleme kalitesi açısından bariz avantajlar sergiliyor; bu, modern yarı iletken endüstrisindeki SiC alt katmanlarının yüksek kalite gereksinimlerine daha uygun. Bu nedenle, yarı iletken teknolojisinin sürekli ilerlemesiyle birlikte, öğütme işleminin SiC alt tabaka düzleştirmenin ana teknolojisi haline gelmesi bekleniyor. Gelecekte, SiC cihazlarının gittikçe zorlaşan alt tabaka gereksinimlerini karşılamak amacıyla işleme verimliliğini ve kalitesini artırmak için taşlama işlemi parametrelerinin daha da optimize edilmesi gerekiyor.