Si3N4 tozu, silikon nitrit toplarının hazırlanmasında kullanılan ana hammaddedir. Düzenli şekilli ve düzgün parçacık boyutu dağılımına sahip tozu elde etmek için uygun işleme yönteminin seçilmesi, Si3N4 seramik bilye oluşturma, sinterleme, işleme ve diğer işlemlerin istikrarlı bir şekilde uygulanmasının temelini oluşturur.
Farklı atomizasyon yöntemlerine göre, Si3N4 tozunun sprey granülasyon yöntemleri esas olarak santrifüjlü sprey granülasyonu, basınçlı sprey granülasyonunu ve iki sıvılı sprey granülasyonunu içerir. Basınçlı sprey granülasyonu Üniform Si3N4 tozu içeren bulamaç, atomizasyon için yüksek basınç altında granülasyon kulesine püskürtülür ve damlacıklar, bulamaçtaki çeşitli bileşenlerin topaklanmasını ve çökelmesini önleyebilen sıcak hava akışı ile hızlı bir şekilde küresel toz halinde kurutulur. Parçacıkların yüzeyindeki çözücünün buharlaşma hızının kontrol edilmesiyle, düzenli parçacık morfolojisi elde edilebilir ve düzgün parçacık boyutu dağılımına, iyi akışkanlığa ve uygun gevşek yoğunluğa sahip sprey granülasyon tozu paketlenebilir. Böylece toz doldurma kalıbının performansı iyileştirilir ve işlenmemiş parçanın yoğunluğu ve tek biçimliliği arttırılır. Bu nedenle, sprey granülasyon tozunun gevşek yoğunluğunun Si3N4 seramik topların özellikleri üzerindeki etkisini incelemek için basınçlı sprey granülasyon yöntemi seçildi.
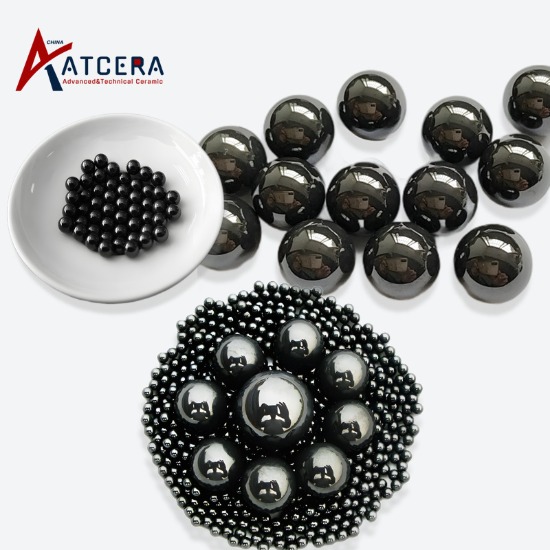
Test Materyali
Si3N4 tozu (partikül boyutu dağılımındaki kümülatif hacim oranı %50 olduğunda, karşılık gelen parçacık boyutu D50=1,5μm, α-Si3N4 içeriği %93, saflık %99,9), Y2O3 tozu (D50=1,8μm, saflık %99,9), Al2O3 tozu (D50=2,2μm, saflık %99,95), vb.
Numune hazırlama
Si3N4â¶Y2O3â¶Al2O3= 92%â¶4%â¶4%(kütle oranına) göre karışım bilyalı değirmene ilave edilmiş, çözücü olarak susuz etanol, çözücü olarak Si3N4 bilya kullanılmıştır. karıştırma ve dağıtma için öğütme ortamı, karıştırma süresi 24 saat, Si3N4 topu ve karışık tozun kütle oranı 3:1 idi. Düzgün karıştırmanın ardından, bulamacın katı fazının kütle oranı %55'tir ve viskozite 4000MPa-s'dir. Püskürtmeli kurutma kulesinin giriş sıcaklığı ve püskürtme plakasının çapı kontrol edilerek farklı gevşek yoğunlukta granül toz elde edildi. Si3N4 sprey granülasyon tozu, kuru bir presle 8.731 mm çapında bir seramik topak halinde preslendi ve ardından atmosfer basıncında sinterleme 1850°C'de gerçekleştirildi, ısıtma hızı 3°/dakikaydı, tutma süresi 1,5 saat ve nitrojen basıncı 9MPa idi. Özellikler hazırlandıktan sonra test edildi.
Sonuç
Aynı parti çamuru ile farklı sprey granülasyon işlemleriyle hazırlanan granül tozun eleme fraksiyonu verileri ve gevşek yoğunluğu Tablo 1'de gösterilmektedir. Seramik pelet hamının yoğunluğu, sinterleme yoğunluğu, bükülme mukavemeti, ezilme yükü, kırılma tokluğu ve Vickers sertliği. farklı gevşek yoğunluğa sahip sprey granülasyon tozuyla preslenen seramik pelet Tablo 2'de gösterilmektedir.
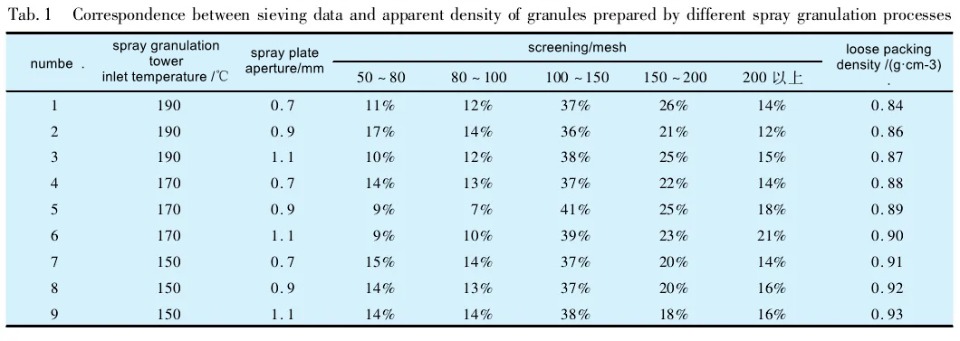
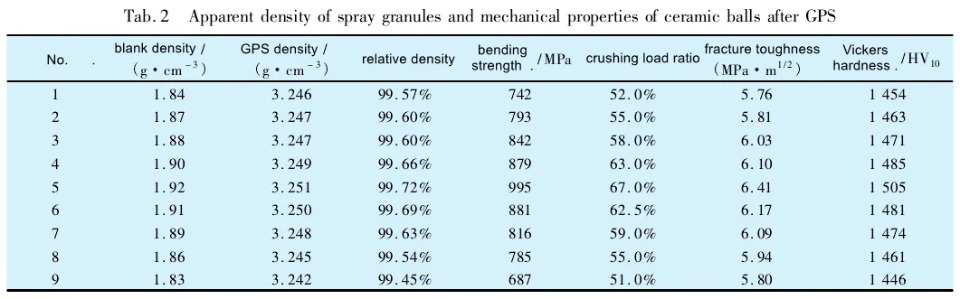
5# granüle toz ile preslenen Si3N4 seramik bilyanın mekanik özellikleri en iyisidir. Çok yüksek veya çok düşük gevşek yoğunluk, tozun presleme performansını ve Si3N4 seramik bilye boşluklarının yoğunluğunu etkileyecek, dolayısıyla Si3N4 seramik bilyaların mekanik özelliklerini etkileyecektir. Mekanizma, gevşek yoğunluğun, preslemeden sonra sprey granülasyon tozunun gözenekliliğini doğrudan etkilemesidir ve gazın boşaltılması zordur, bu da sinterleme işlemi sırasında sinterleme yoğunlaşmasına elverişli olmayan parçacıkların ve maddelerin uzun göç mesafesine neden olur.
5# Si3N4 sprey granülasyon tozunun parçacık morfolojisi katı ve küreseldir (Şekil 1).
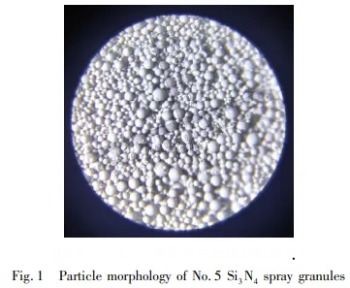
Si3N4 seramik top GPS'in 1# ~ 9# sprey granülasyon tozuna göre mikro yapısı Şekil 2'de gösterilmektedir. Granülasyon tozunun gevşek yoğunluğunun artmasıyla, GPS sonrası Si3N4 seramik topun içindeki gözeneklerin sayısı önce artar, sonra azalır. ve Si3N4 seramik topun yoğunluğu önce artar, sonra azalır.
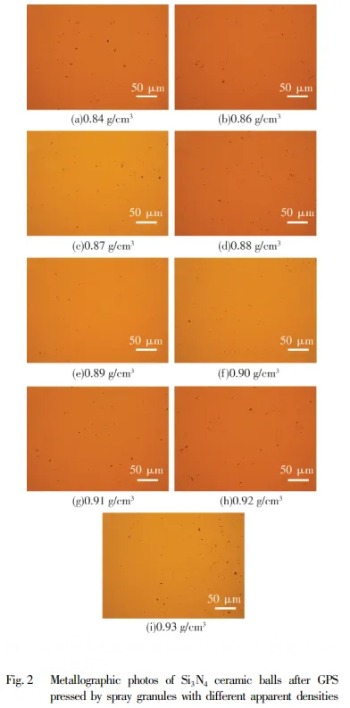
SEM, en iyi mekanik özelliklere ve zayıf mekanik özelliklere sahip Si3N4 seramik topların kırılmış örneklerinin mikroyapısını ve tane kırılma morfolojisini gözlemlemek için kullanıldı. Şekil 3'te görüldüğü gibi Si3N4 seramik toplarının yoğunluğu, granül tozun gevşek yoğunluğunun artmasıyla önce artmış, daha sonra azalmıştır. Çok yüksek veya çok düşük gevşek yoğunluk, düzensiz tane büyümesine ve iç gözeneklere yol açacaktır.
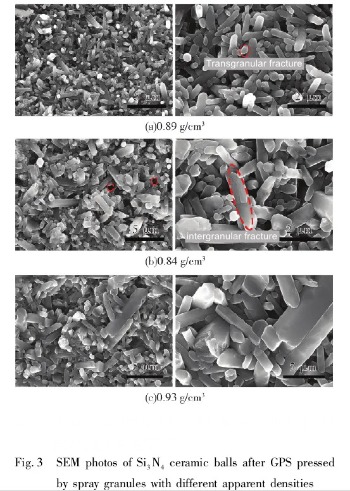
Sonuç
Hammadde olarak Si3N4 tozu ve sinterleme katkı maddeleri olarak Y2O3 ve Al2O3 ile, sprey granülasyon tozunun gevşek yoğunluğunun seramik bilye sinterlemesinin yoğunlaşması ve mekanik özellikleri üzerindeki etkisi analiz edildi. Aşağıdaki sonuçlara varıldı:
1) Si3N4 seramik bilye boşluğunun yoğunluğu, granül tozun yığın yoğunluğunun artmasıyla önce artar, ardından azalır. Gevşek ambalaj yoğunluğu 0,89g /cm3 olduğunda Si3N4 seramik bilye en yüksek yoğunlaşma derecesine ve en iyi mekanik özelliklere sahiptir.
2) Sprey granülasyon tozunun kütle yoğunluğu 0.89g /cm3 olduğunda, oluşturulan Si3N4 seramik topu en küçük gözeneklere, tekdüze tane boyutuna sahiptir ve esas olarak transgranüler kırılma modunu benimser.